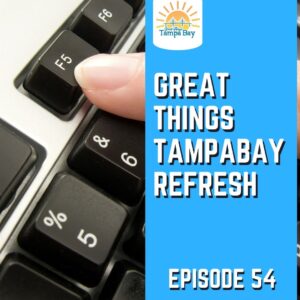
Episode 54 – The Refresh (Updates on all ~50 Great Places We’ve Discussed!)
Episode 54 – (Updates on all ~50 Great Places We’ve Discussed!) Alexa, play Great Things Tampa Bay Show Notes After a significant milestone (or time
Few things spark as much imagination as a musical instrument. Give a toy guitar to a 4 year old and watch what happens. It’s like we’re both with music in our soul!
Local Luthier (that’s someone who builds guitars) Erdem Koca of Koca Guitars has been building instruments for years. Listen in as he shares some of the secrets of his craft with us.
Transcript at the bottom of the page!
How to write many ways you can shuffle a deck:
80,658,175,170,943,878,571,660,636,856,403,766,975,289,505,440,883,277,824,000,000,000,000
52!
Estimated: 8 with 67 zeros after it
8.06e+67
Unfortunately Ania didn’t give me any additional information, but thought the song was great and wanted to share!
Episode 54 – (Updates on all ~50 Great Places We’ve Discussed!) Alexa, play Great Things Tampa Bay Show Notes After a significant milestone (or time
Episode 53 – Episode 53 – Delco’s Cheese Steaks – Clearwater / Dunedin Alexa, play Great Things Tampa Bay Show Notes Delco’s Cheese Steaks are
Episode 52 – Replay Pinball Museum and Olive the World – Tarpon Springs and St Petersburg Alexa, play Great Things Tampa Bay Show Notes Replay
Episode 51 – How to Get a Free Composting Bin for St Pete Residents! [FREE!] Alexa, play Great Things Tampa Bay Show Notes Want to
Episode 50 – Does Great Things Tampa Bay write paid puff pieces? [HATE MAIL] Alexa, play Great Things Tampa Bay Show Notes Does Great Things
Episode 49 – 1812 Overture with Buccaneers Cannons at Raymond James Stadium by Florida Orchesta [2019] Show Notes Listen as The Florida Orchestra performs the
Thinking about buying or selling a home in Tampa Bay?
Put someone who has lived, worked, listed, and sold homes in almost every neighborhood in the Tampa Bay area to work for you today!
Kyle: I’m here with Erdem Koca of Koca Guitars. And his favorite guitar is the one that he built. Hey everybody, this is Kyle Sasser, “Great Things Tampa Bay,” and this is episode 30. And today, we’re doing an interview with a local guitar maker that is a luthier for those with the vocabulary app on your phone. So, the gentleman I’m interviewing today his name is Erdem Koca and he is from Turkey originally, Istanbul, and he’s been making guitars for years, currently based in Tampa and does some amazing work. And I found him on Instagram, Koca Guitars. He’s also on Facebook, and yeah, does some amazing work. He’s also partnered with some other local luthiers here that are doing some amazing things. And yeah, I hope you enjoy the interview. It was definitely interesting and eye opening and a pleasure to do.
Hi everybody, this is Kyle Sasser, “Great Things Tampa Bay,” and I am here with Erdem Koca of Koca Guitars. And he’s originally from Istanbul, Turkey. He was involved in the film industry for 8 years and has been a luthier for 10 years. And for those of you that don’t know, a luthier is someone who builds musical instruments, and in this case, guitars. And yeah, he’s also played guitar for 30 years and his favorite guitar is the one that he built. Does all that sound right and accurate?
Erdem: Well, yeah. We obviously have inspiration from all the great brands and models from the ’50s and ’60s but we’re trying to refine them, make it our own.
Kyle: Yeah. Touch them up a little, customizations here and there, and just looking around the workshop here, just beautiful, beautiful woods and craftsmanship.
Erdem: Thank you.
Kyle: Well, let’s start at the beginning here. How did you get involved with making guitars?
Erdem: It is funny. When you’re a guitar player, you go to workshops all the time, you know, sew up a pick up, make some adjustments to the neck, stuff like that. And I did that for 20 years and I really like that environment, you know, those guys working slowly with the instrument and make it perfect for the player. And also, you know, creating something from lumber, a functional and beautiful instrument, which will, you know, create music. It’s, you know, unbelievable stuff. So it’s like one summer when I was in the film industry, I was like maybe I should try this. I should apprentice with a master. And I did that and I couldn’t leave the workshop after that.
Kyle: Yeah. You know, that’s definitely a good indication that it’s something that’s gonna be good for you long term is, you know, you develop that passion so quickly.
Erdem: True. I don’t know if it’s an over-statement but luthier is not a choice, it’s a calling, they say.
Kyle: Yeah. And, you know, it’s a little bit of mystery about, you know, people who craft musical instruments. So, what’s one thing that you wish that everyone knew about instrument building?
Erdem: Just listen to your luthier. Listen to him closely, just trust him. And because we’ve been doing this all our lives from, you know, I don’t know, 10 years, 20 years, whatever the time is, starting from early in the morning to late at night. This is what we do, this is what we think. So, obviously, all guitar players, they have something in mind, they’re playing their instrument, we have respect for that, we are guitar players ourselves, but we are doing this for a living so trust us, listen to us, listen to our explanations and recommendations.
Kyle: Yeah. So it’s like if someone was building a house, you wouldn’t just, you know, command people to put things, you know, here and there. You would actually, you know, respect the fact that they know how to do the framing and to put the roof off without it flying off in the next hurricane.
Erdem: True. Exactly. So because we had those crazy ideas ourselves as well, and we tried them and we failed so, you know, you can trust us.
Kyle: Yep. So what’s the craziest thing you tried that didn’t work out?
Erdem: Just, you know, trying different woods for different parts of the guitar. Trial and error and, you know, some things. It’s a miracle, wow, it’s so great, but then otherwise, you know, it’s a failure. So we do this, we try it, and this is not only me, obviously. There are maybe thousands, tens of thousands of luthiers around the world in every region, and they’re using all different types of woods for all different types of musical instruments. And now that we have internet and social media, we’re sharing all that information with each other. And we’re getting that information, we’re thinking about it, we’re dreaming about it. We’re designing in our dreams and everything.
Kyle: So, do luthiers share both their successes and their failures with…?
Erdem: Some of them, some of them.
Kyle: Some do, some don’t?
Erdem: Like in everything, yeah.
Kyle: Well, a lot of times, you know, because I’ve been…I’ve had a few businesses and a lot of times it’s better to know what’s failed than what’s succeeded because it’s like you can spend most of your life following failures but it’s like, you know, somebody else has tried it and they’re like, you know, you can kinda cut that, unless you have some novel approach this is gonna make the result different.
Erdem: True.
Kyle: Yeah. Failure…and just as an entrepreneurs, failures are just, you know, steps along the path.
Erdem: As important, yes.
Kyle: Yes.
Erdem: As important as the successes. Well, the successful part is if you just examine those guitars, they’re still with us for even after 50, 60 years. Some guitars are still with us, they’re not changed that much, so obviously, those are the successful designs. But then they’re, again, from 50, 60 years ago so we have to change them a little bit. I mean you’re not using the same car, you’re not using the same phone, you’re not using the same technology on any other side of your life, so why in guitars? We have to refine them, we have to make them better if we can, and that’s what we’re trying.
Kyle: So what’s an example of a new technology that’s a lot better than it was 50 or 60 years ago?
Erdem: For example, glues are much better now, much stronger. You’re not using the hide glue anymore.
Kyle: Sorry. I have done some woodworking in my day, so hide glue is the pain in the ass.
Erdem: Well, some luthiers are still using it. For example, violin makers are still using hide glue. Some classical guitar makers maybe are using it for gluing the top, stuff like that. But electric guitar making, we don’t use it anymore, we have stronger glues. Or maybe we use carbon fiber neck reinforcements in the neck along with the truss rod just to make the necks more strong and stable, especially if you’re in Florida with all the humidity and everything.
Kyle: Yeah. Things move a lot down here. Now for those of you that don’t know, the truss rod is…
Erdem: It’s a rod in the neck to adjust how the neck is straight or if there’s a little bit relief on it to make it comfortable for the player. We use that for adjustment but sometimes it’s not strong enough, especially after maybe 5, 10 years. We want neck to be stable so those carbon fiber rods are making that. We glue it on with epoxy.
Kyle: Interesting.
Erdem: Yeah, that’s just an example.
Kyle: Actually, I was gonna ask if it was done like a fiberglass lay up where you laid on it if it’s rod, that’s epoxy then somehow.
Erdem: That’s being done before, too. Just, you know, composite material guitars, aluminum guitars, you know, resin guitars.
Kyle: Luthiers like trying things.
Erdem: Yeah. We’re trying to…you know, good thing about electric guitar design is it’s free, just like rock and roll. You know, anything you come up with, if it’s good it can stay. In classical music world, it’s different.
Kyle: Yeah. They’ve been around a lot longer than electric guitars as well.
Erdem: True. And the repertoire is the same, so playing style of that repertoire has to stay the same as well. So the instruments should not change in their mind as well. But, you know, pop music, rock music is not like that. We like change so we can change and redesign or…
Kyle: Frequent change.
Erdem: Yes. We can redesign our instruments and we can try different materials, no problem.
Kyle: Yeah. It’s fascinating, fascinating. All right, so is the bass guitar the unsung hero of a rock band?
Erdem: Well, yeah. There are many jokes about bass players and drummers. But yeah, base is so important with the drums. It’s foundation of the song most of the times. But you don’t hear it that much if you don’t listen to it. It’s, you know, something like that but it’s really important part of the song and the band. I mean you understand if the bass player is not playing. You will figure out there’s something, it’s hollow, you know, it’s empty sounding, whatever.
Kyle: It’s almost like the heartbeat to me a lot of times like when listening to music. Like I know the drums are obviously more of a heartbeat but to me like the bass actually kinda carries a lot of it.
Erdem: True. If he’s not playing for some reason, if the jack input is a problem, I’d say if you don’t hear him, you will understand, there’s something wrong with the sound. But if he’s playing, it’s no big deal.
Kyle: Yeah. And you do make custom-based guitar.
Erdem: Yes.
Kyle: Tell us about the guitars that you make here.
Erdem: Okay. So I started this 10 years ago and I’ve been making electric guitars and bass guitars, and semi-hollow electric guitars for 10 years. I made about 100 instruments so far, it’s my 10th year now. I also repair guitars. The first guitar I made was a classical but just because of the fact I mentioned, I understood that I have to make that design again and again and again, and I can’t change that design. Otherwise, the players, the conductors, the people in that community is not happy.
Kyle: It’s a classical as like an acoustic guitar, right, with the big body and all that stuff. The hollow body and…
Erdem: Yes, yes. So that’s why I picked electric and bass so that I can make my own designs, make my own touches, and that’s what I did. I have seven, eight designs, models. So I make, you know, double cutaway guitar, single cut guitar, semi-hollow guitar, same thing with bass guitars. You know, I’m trying to reach the blues guitar player, the rock, the metal guy, and the jazz guy, but I’m trying to stay in just making electrics and basses so that I can be a master on building it. Because there are so many types of guitars. You have the acoustics, you have the classical, you have the fretless, you have the jazz, I mean you have the 12 strength, fretless, semi-acoustic bass guitar.
Kyle: And then what was the one that I couldn’t think of the name of?
Erdem: The Dobro maybe. So there are so many instruments and if you are making only a couple instruments per month, I mean how are you gonna be a master of all of those things? I mean just lifetime of working so I picked one road and I’m trying to, you know, perfect that design.
Kyle: Awesome, awesome. So you’re here at Guitar Repair of Tampa Bay.
Erdem: Yes.
Kyle: And this is your workshop and you’re also partnered with a couple other gentlemen as well, right?
Erdem: Yes.
Kyle: They’re involved here?
Erdem: Yes. So it’s pretty awesome. When I moved here like eight months ago from Istanbul, I was just visiting local luthiers here. And I run into these guys and this place, Guitar Repair of Tampa Bay, Mick Donnor and Ben Schafen, they’re awesome people. They have been working in the industry for 35 years. They’ve worked in major brands like Gibson, Dean, Peevay, Washburn.
Kyle: Okay, so yeah.
Erdem: And then they open their workshop like maybe 10 years ago here ago. And they repair guitars here and they make guitars here, so I just, you know, started talking to them and they were like, “Yeah. You got a space here if you wanna work with us.” And that was awesome for me, they welcomed me here. So I’ve been working here maybe for four months. I’m repairing guitars here and I’m also making guitars, and I just shipped a guitar to Istanbul, by the way.
Kyle: Awesome, awesome. Sending it back home.
Erdem: Yeah, yeah.
Kyle: Yeah. Well, speaking of Istanbul, you did say that you did make instruments for famous performing artists over there. I wanna try and not murder this name, Jim Tunges [SP].
Erdem: Tunges. Well, yeah. Those guitar players are, you know, nationally famous like Jim Tunges, like Elmer Coola [SP], Saidy Mashik [SP]. Guitar players and bass players, they are famous in Turkey. Obviously, you don’t hear them here. So much talent here as well, so they’re not globally famous. But yeah, I was lucky enough to make guitars for the bedroom guitarist and also the stadium guitarist.
Kyle: Yeah. That’s good. You know, like to me that’s proof of, you know, that your craft is…
Erdem: Hopefully.
Kyle: …at the level it needs to be.
Erdem: Hopefully, yeah. I was just texting with a customer this morning. He wants to replace the pick-ups so I’m gonna send him some pick-ups from here, so a guitar that I made over there so it’s a process.
Kyle: Awesome. Well, tell me about your favorite guitar currently.
Erdem: Well, honestly, all those guitars, like the Fenders, the Gibsons, the PRS, they’re awesome. They’re the standards. But then there’s many small time builders around the world, and I’m following them on social media, and they’re awesome because they are doing something different and they are pushing the envelope. Like Collings in USA, I really like their work, they’re amazing. Or Matsuda, an acoustic guitar maker from Japan, or Michael Spalt from Germany. I mean you can be anywhere in the world nowadays, thanks to internet and all those connections, and you can make those beautiful, beautiful instruments, different designs. It’s like they’re turning it into an art form almost. So, yeah. Many small time boutique makers are making a difference right now.
Kyle: Yeah. So what’s the difference between like, let’s say, like a Fender or Les Paul, and like a guitar that someone would get from you?
Erdem: The major difference is customization. So let’s say you’ve been playing the guitar for 10 years, 20 years, and you played all those guitars, the Fenders, the Tellys, the Les Pauls, and there are some things that you like on those guitars but you want to combine all of those features on one guitar. That’s where we step in and make a dream guitar for you. So it’s not gonna be the best guitar for everyone but it’s gonna be the best guitar for you.
Kyle: So it’s definitely almost like a custom-tailored suit?
Erdem: Exactly. It’s tailored to your needs, to your wants, to what you like aesthetically, the visuals, the tone, the ergonomics. Everything, we consider, and we talk to the customer. You know, sometimes it takes 10 minutes if the customer knows what he wants exactly. Sometimes it takes months, you know, back and forth trying to figure out what he really, or she really wants on, you know, the wood choices, the pick up choices, all the hardware, how it should look like, how much it should weigh. You know, it’ so funny. Some people like really light guitars, some people want especially heavy guitars.
Kyle: There’s a lot of like…and if you don’t play guitars a lot you probably don’t…you know, when you see them from the front they all kinda look the same. But just, like the way that the neck feels in your hand and like the distance between the strings and the fret board, which is called like the action, right?
Erdem: Yes.
Kyle: See, like that can be either very high where you have to put a lot of power into it to bring the string down. So that is all customized by a luthier.
Erdem: So you maybe understood by now, I’m a guitar fanatic. You know, I’ve been playing…
Kyle: I do.
Erdem: I’ve been playing the guitar for so long and I love this instrument. I’ve been thinking about this, like why is the guitar the most popular instrument in the world? It’s not the best design instrument, it’s not the perfect instrument for musical education, maybe the piano is better, so why is it so popular? I think it’s because you can personalize it that much. You cannot personalize a violin or a piano that much.
Kyle: Do they even do custom paint on a Steinway? I think they all come in black.
Erdem: I think it’s against the law to do that. So, as you’re saying, all those small design features, customizations are, we are able to do them on the guitar. And those little touches make a lot of difference to the player.
Kyle: Yeah. And obviously, you can make a lot of great music with it, too.
Erdem: And all kinds of music, that’s the great part. I mean from, you know, technical death metal to, you know, folk music. From blues to progressing music, like everything and anything you can play with the guitar, that’s the beautiful part.
Kyle: And even Cracker music, right?
Erdem: Yes, the Crackercaster.
Kyle: Yep, so yeah. So he was telling me this in our pre-interview interview. So they make a custom guitar here that’s pretty special to the Tampa Bay area. So would you like to tell us a little bit?
Erdem: Yes. Ben and Mick, the owners of this workshop, they have this brand called Crackercaster. So Crackers were the first cowboys in Florida.
Kyle: So back when it was all cow country here, they were the cowboys in Florida were called Crackers because they crack whips behind the cows.
Erdem: Exactly. So they got the name from that and the idea is they’re using all local woods from Florida. So for the body they’re using Florida cypress, for the neck they’re using Florida ash, and for the fretboard they’re using Florida rosewood, which is from Davis Island, which is amazing.
Kyle: Because David Island is not exactly forested.
Erdem: No.
Kyle: So how did they come about…
Erdem: They planted some rosewood trees, maybe ’50s. I’m not sure about the exact date, but they planted some rosewood trees on David Island because the flower of that rosewood tree is beautiful.
Kyle: Yeah, yeah, they’re beautiful.
Erdem: Yeah. So when a storm comes, when the tree goes down, we salvage that wood and make fretboards out of it for our Crackercaster guitars. And the amazing thing is Ben and Mick, who worked in this industry for 35 years each, make those guitars here. So they’re made in USA guitars from local woods, pick-ups are made in California, and all the hardware is very good. And they have a great price point, which is our area code, 813. Starting from $813, made in USA guitar, amazing.
Kyle: So for $813, you can have a handmade, locally made guitar made from all local woods and the fretboard comes from Davis Island.
Erdem: You summed it up great. Yeah, that’s…
Kyle: And I’m gonna have a picture of this up on the website. It’s pretty awesome.
Erdem: And it’s pretty popular, too. They have like 20 in order. They’re trying to finish them but, you know, people loves this guitar really.
Kyle: Yes. Well, it’s awesome, it’s awesome. So I have to ask because this was in the news recently. Do you have any smash-proof guitars?
Erdem: There’s no such thing as far as I know.
Kyle: All right. So for those of you that don’t know, the movie “Hateful Eight” that came out a little while ago, something like that, they were lent a 145-year old guitar by Martin, I think it was?
Erdem: Yeah.
Kyle: Yes, so it’s this old acoustic guitar and basically Kurt Russell smashes it.
Erdem: There’s a pretty funny clip on YouTube, people should watch this.
Kyle: Yeah. Well, I’ll put a link to it in the show notes here. So it was Kurt Russell and…
Erdem: Jennifer Jason Leigh.
Kyle: And do you wanna paint the picture of the scene for us?
Erdem: Yeah. So they’re in a bar and Jennifer is playing the guitar. And she’s a guitar player actually, she’s playing and singing, she’s good. But then Kurt Russell, for some reason, gets upset and picks the guitar up and just smashes it, but it’s an old, old, vintage, very valuable guitar, 140 years old. And apparently, he doesn’t know it’s the real thing, but it is. So, all those companies, Martin and Gibson, they have a new rule now. They’re not lending their instruments to Hollywood anymore.
Kyle: Yeah. And when you watch the scene like the look on Jennifer Jason Leigh’s face. She’s like, “Oh, my gosh.”
Erdem: Oh, my god. I think she knows it’s the real deal. Maybe Kurt Russell doesn’t know or maybe he knew and just did it anyways for the sake of the movie, I don’t know.
Kyle: He seems like a guy that just does not give a shit, so maybe.
Erdem: Maybe.
Kyle: So, all right. Well, okay. Well, is there any challenges you’ve experienced like as an immigrant starting up a new business here in…?
Erdem: No, not really. I mean this country is built by immigrants so it’s same process for me. I love it here, honestly. I love Florida, too. And, you know, the reason I picked this place when I moved to USA is not only my brother has been living here for 15 years but the weather is nice, people are super nice, and that lifestyle…I lived in Istanbul, 15 million people city, for so long.
Kyle: Yeah, it’s a major metropolis.
Erdem: Yeah. I didn’t wanna go to New York or L.A. You know, big cities, you know, I’m over it now. So I love Tampa, Tampa Bay area. And no, I don’t have any problems. People are always welcoming me here and I love it.
Kyle: That’s good, that’s good. So, temperature-wise, how do we compare to Istanbul?
Erdem: We have four seasons there.
Kyle: Oh, okay, yeah.
Erdem: Not here.
Kyle: Yeah, we are nowhere near that.
Erdem: No, but I love hot weather. I’m built for hot weather. I was born on July on like 85 degrees so I’m used to it, you know.
Kyle: It’s a nice balmy Mediterranean day.
Erdem: Yeah.
Kyle: We love it when we get 85 here. I don’t know if you know that or not. Eighty-five is winter. So, if you had someone that was looking to get into instrument making today, how would you tell them to go about it?
Erdem: There are a couple of ways of doing it. There’s no one correct way. You can apprentice with a good luthier for sure, that’s the common way of doing it. There are some good schools too you can go for a couple of months or a couple of years. That’s a very good way of doing it as well. But then most important thing is it has to be in you. You really, really have to want to do this. So I didn’t go to a school, I didn’t study with a guitar maker. I apprenticed with an [inaudible 00:24:13] maker. So I learned guitar making by myself, internet, books, YouTube, reverse engineering. So if you have that itch in you, you’ll do it anyways. But the best ways, I think, is working with a master, apprenticing with a master, or just studying in a school.
Kyle: Are you taking on any apprentices here currently?
Erdem: Sometimes, you know. It’s really hard to find people who really devotes their life into this. It’s not something you’ll do for half an hour and you’ll become master, it’s not like that. Woodworking is really hard to master. And…
Kyle: Yes, so yeah. So I do have some experience woodworking, and yes, I saw a picture on one of the woodworking forums I’m on. This guy had built a completely enclosed, fully mitered floating shelf. So it’s like…and a miter, it’s like 45-degree corner so you don’t have to show the ingrain. So he had miters on all the corners and then on the face to inset the face, which I have attempted. And it is extremely difficult to get it to look right without a lot of putty, which is my go-to. So to be able…and a guitar is very important. Everything has to fit together because it’s under a lot of stress.
Erdem: True.
Kyle: You know, from both the strings and the…
Erdem: Tension of the strings, yes.
Kyle: Yeah.
Erdem: True. It has to be really strong, the neck and the body has to fit each other perfectly even if it’s set neck or bolt-on neck, it doesn’t matter. It has to be a tight fit. The neck has to be consistent and the body has to be balanced for the player to play. I mean when you’re making a table, you consider some ergonomical features. But when you’re making a guitar, then you have to think about the tone as well. So, everything changes between 45 millimeters and 50 millimeters.
Kyle: Yeah, because the wood is vibrating a little differently at that point.
Erdem: Exactly, yes. And when you’re making a custom guitar from different woods, trying different pick-ups on it, and certain players playing, it’s an adventure.
Kyle: Yeah. That’s awesome. How can people get in contact with you?
Erdem: Social media is the best way. Koca Guitars on Facebook and on Instagram. I’m trying to be pretty busy. And also, as I said, we’re in Guitar Repair of Tampa Bay. We’re repairing and making guitars here so people are welcome to take the tour here.
Kyle: Awesome, awesome. And we’ll have all those details in the show notes. Sir Erdem, thank you so much.
Erdem: Thank you for having me here.
Kyle: So, again, I’d like to thank Erdem for taking the time to sit with me and do that interview. Definitely, it means a lot to me and I can tell you, like sitting in his workshop and office, and just seeing the sheer number of guitars and craftsmanship that was in that place, it was very humbling. You know, I’ve tried to do some woodworking myself in the past and I can tell you that what he does is not easy. It’s definitely a craft and a skill that takes years to perfect. And yeah, they’re beautiful. And also, yeah, the Crackercaster, we do have pictures of that. It’s on the show notes, it’s also on the website, greatthingstb.com. So go over there, take a look, or follow the link in the show notes.
And now, segment two, your fact of the day. There are 80 million, million, million, million, actually I don’t really know how many millions this is. It’s 80 with 67 zeros after it. So there’s that many ways to arrange a deck f 52 cards and that is more than the number of atoms in the earth. All right. So that’s gonna wrap up episode 30 for “Great Things Tampa Bay.” I hope you’ve been enjoying these past 30 episodes. Be sure to go back and take a listen to some previous ones. We got some good stuff back there that’s pretty much applicable year round. You know, except for like the State Fair Florida Strawberry Festival. But, you know, all of the other stuff is still great. Hall on Franklin, still amazing. Mount Dora, still there. And Chief’s Creole Cafe is still killing it with the Creole food over in St. Petersburg.
So do be sure to go back and listen to our archives. If you have any questions or suggestions, please go to the website, greatthingstb.com, and along the top there you’ll find some links to submit your favorite restaurants or, you know, maybe…you know, this is a guitar episode so if you are a musician or you know a musician, I actually do…you know, I like to promote local musicians at the end of the podcast so please just go there and submit your songs. And, you know, you might be featured at the end of one of my podcast episodes. And, you know, you get like a shout out and all that stuff. Let’s see what else.
Also a local realtor, and if you’re looking to find your own great place in Tampa Bay, I would love to help you out and find a new home for yourself. If you’d like to reach out to me in that aspect, again, just go to the website, greatthingstb.com and at the top you’ll find the link to contact me for real estate-related items.
Playing us out today is Anya with “Slide,” which is a very fun kinda disco beat, kinda takes you back to that ’70s thing without all of the, you know, the downside, or I guess upsides in some manners, but you know. But very fun, it’s got that funky ’70s beat and I’m just gonna stop trying to describe the song because I’m not doing a very good job. Anyway, thanks for tuning in. Be sure to share us with a friend. And if you’re interested in learning more about Koca Guitars, or if you like this song, there’s gonna be a link in the show notes, so just pull up those details and you’ll find it. So anyway, thanks again, and I’ll see you next episode.
[music]